Evolution of Pixels: From Lamps to SMD LEDs
Much has been written about LED screens. During 20 years of their history, screens changed significantly. We decided to devote this article to the evolution of the key element in a digital screen, to the pixel.
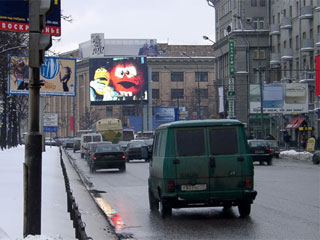
Electronic information signs and dynamic sound and lighting equipment served as prototypes for first digital screens. Initially they were all based on incandescent lamps. The main shortcoming of lamps was short lifespan – upto 500 hours. After 500 hours of continuous operation 50% of lamps could fail and needed replacement.
Working conditions on digital screens are the most unfavourable for lamps: a constant “on-off” mode. To extend the life of lamps a simple method was invented: to reduce the feeding voltage. Lamps now worked longer but another problem surfaced: with lower power the visible spectrum shifted into the red zone. One monochrome screens this could be easily disregarded but created grave problems for multicolor and full-color screens.
To turn a lamp screen into a multicolor installation was fairly easy: standard white lamps were either painted into red, green, blue and light-blue or placed behind color filters. Light filters absorbed a large part of light radiation and to keep the screen brightness it was necessary to place a reflector behind the lamp. The quality of colors, white balance and brightness of the screen fully depended on the quality of lightfilters and reflectors, their precise positioning. Naturally, such systems were complex in manufacturing and assembly, bulky and expensive.
Another serious shortcoming of incandescent lamps was their high power consumption. For example, typical screens with three inch pitch (76.2 mm) used lamps for auto industry 1250X (Uwork=13.5V, Icons=0.37А, lifespan 500 hours). One pixel contained 4 such lamps.
At 12V voltage one pixel consumed 16W, and one square meter of such screen consumed nearly 3kW of energy. Thus, a relatively small screen with 112x84 pixels and image area of 54.5 square meters turned into a powerful energy plant with maximum power consumption (white peak) of 165kW.
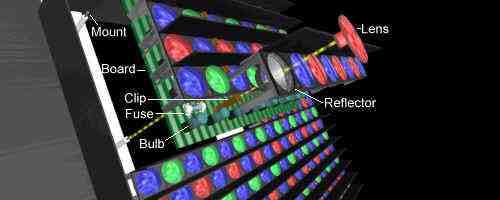
Lamp screen module
This had some peculiar effects: in winter the snow in front of the lamps screen melted and turned to rain, while in summer such screens overheated. A powerful ventilation or airconditioning system was needed to maintain normal operation of the screen. This increased power consumption even further (nearly 1/3 of the screen power consumption). Ventillation system required regular check-ups and cleaning. The costs of screen maintenance were thus astronomical.
In spite of high energy consumption, the total brightness on lamp screens was insufficient for daytime operation, about 2500 nits. To increase brightness by placing lamps closer together was impractical: any increase in resolution lead to increase in power consumption and significant problems with heat dissipation.
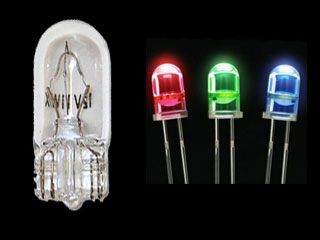
Bulb size 10.2х26.9 мм
Another serious problem of lamp screens was a fire hazard. With high power consumption and high heat emission, high currents and powerful fans, plastic components and miles of cable – the probability of fire was tangible. Various fire prevention means led to lower screen reliability and higher production costs. At this stage in technological development, to turn digital lamp screens into massive and commercially attractive product was impossible.
Screen manufacturers were interested in LEDs as potential replacement of incandescent lamps. Initially, they started experimenting with monochrome or two-color displays by combining red and green LEDs. New light emitting elements allowed to significantly reduce power consumption, increase brightness and reliability.
First LED screens were created as a simple replacement of lamp screens. Structurally they were based on clusters widely used in information signs. A cluster is a unit that includes LEDs (in various combinations), frame (box) and connecting cables. This structure is convenient in maintenance and allows easy replacement of a failed cluster. Though manufacturers guaranteed long life of individual LEDs (50 000 hours, sometimes even 100 000 hours) in reality few manufacturers reached such excellent parameters. Among those few are Nichia, Toyoda Gosei, HP/Agilent, Cotco/Cree. Clusters were an intermediate stage, some other technological solution was needed.
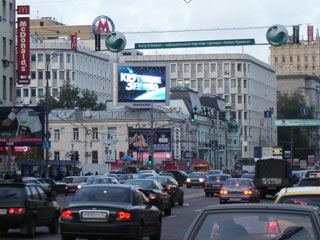
The first high brightness blue LED was demonstrated by Shuji Nakamura of Nichia Corporation in 1990. By 1993 blue LEDs were mass produced and available for the market. Ten years later, in 2002, Nichia was a world leader in LED manufacturing and 60% of its production were blue LEDs. Prices stabilized and manufacture of full-color LED screens became viable.
First LED screens have relatively low resolution. Typical lamp pixels of 76.1 mm (3 inches) were replaced by LED pixel of 38.1 mm (1.5 inches). To maintain or even to increase the brightness (while maintaining the white balance) of the image area it was necessary to arrange a cluster of several LEDs, for instance, 4 red, 4 green, 2 blue. This pixel consumed about 1W, or 16 times less energy than a similar lamp pixel. Thus, a screen with 2 times higher resolution would provide a much better image and has 4 times lower power consumption. More actually, since ventilation system was no longer required.
Though a step ahead compared to lamp screens, LED screens based on clusters had some serious shortcomings: too many connectors reduced reliability of the system, large number of small components resulted in increased cost and longer assembly time.
The task of increased reliability and lower cost was solved by placing large number of LEDs in one module (64, 128, 256 and other options). Any failed component on a module (LED, passive component, or driver) required replacement of a whole module. This was especially true in relation to outdoor screens: modules had to be protected against rain and snow by compound that hermetically sealed the PCB.
![]() |
![]() |
4R2G2B and 2R2G1B LED clusters | LED screen with 2R2G1B pixels |
As pixels were growing smaller and were placed tighter on a PCB, the composition of the pixels drastically changed: from a cluster of 7-12 LEDs to basic 2RGB-pixels (2 Red, 1 Green, 1 Blue), and later – to RGB.
The use of LEDs allowed to move away from a 12V systems (lamp screens) to 5V. This change also led to lower power consumption and better heat dissipation. 2RGB or RGB pixel consumed approximately 0.3W, the whole square meter of a screen based on a popular 19 mm pixel pitch consumed 839 W at the peak of white. A 6x4 meter screen with 320х240 resolution consumed only 20kW (a drastic reduction compared to lamp screens).
As the pixel grow physically smaller, it became smarter: developers of LED screens started using various brightness and resolution enhancement techniques. Our magazine published articles about virtual or dynamic pixel repeatedly: “Virtual pixel: Promotional trick or image improvement”.
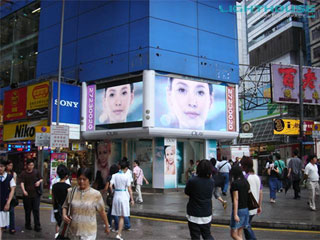
Photo credit: Lighthouse Technologies
At some point the miniaturization of pixel stopped due to technical bottleneck. Standard 5 mm oval DIP LEDs used to form an RGB pixel could not be placed tighter together: some free place on the board was needed for other electronic components and connectors. An intermediate solution was to use 3 mm LEDs but these later were rejected because of low stability.
All future hope to change LED pixel were concentrated on an SMD LED (surface-mounted). Once invented SMD LEDs were meant for indoor applications only, because humidity negatively affects their operation.
Different SMD LEDs were tested: single color LEDs, large and small sized LEDs. But the most promising option of 3-in-1 SMD LEDs became most popular. At present, the physical size of an SMD LED is limited by technological processes of surface-mounting machines to 4 mm.
One of the main shortcomings of SMD LEDs was bad contrast. Fully switched off SMD screen looks whitish because of the white background for LED chips. The efforts of developers were focused on solving the contrast problem – and finally the solution appeared in the market in the form of so called black face SMD.
![]() |
![]() |
Modern outdoor 12 mm pitch LED screen in London: 12.3x3.5 m Photo credit: Lighthouse Technologies |
Black face SMD LED module Photo credit: Ekta |
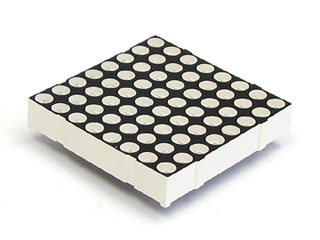
Parallel to SMD, another indoor screen technology was developing - Dot Matrix. LED chips are arranged in 8x8 matrix: a minimalistic approach that offers economic solution. As with standard SMD LEDs the main shortcoming of Dot Matrix technology is the whitish background and poor contrast. While the white background serves as a reflector and increases the brightness of the screen, it leads to poor quality of image at low brightness levels.
Comparative tables of power consumption in the evolving pixel
4 Lamps Pixel | DIP LED cluster | DIP LED pixel | DIP LED pixel | SMD LED 3-in-1 | |
---|---|---|---|---|---|
RGBbrB | 4R4G2B | 2RGB | RGB | RGB | RGB |
1:1 | 1:4 | ||||
16W | 1W | 0.4W | 0.3W | 0.3W | 0.075W |
As we see, in less than 20 years pixel changed and modified significantly. Obviously, this is not the end of the road; probably, only the beginning of the pixel story. But whatever the case, we have to know this story well.